With construction workers scarce, homebuilders turn to robots, software
- usatoday.com
- Jun 26, 2018
- 6 min read

Photo shows Florante Fernando operating a wall processing machine which fastens, trims, and cuts openings in sheathing.(Photo: Nick Panetta, Blueprint Robotics)
BALTIMORE – The construction of an American house embodies the spirit of the nation’s workers and the dreams of its citizens.
It’s also perhaps the least-efficient endeavor in the U.S. economy.
Dozens of workers turn a plot of land into a small factory, sawing wood, nailing it together, cutting holes for windows, running wires and pipes and installing drywall and other finishes. Four months or so later, voila: A home for generations of families.
Now, a worsening construction worker shortage that has driven up home prices is beginning to turn that routine – largely unchanged over the past century – on its head.
At a sprawling factory owned by Blueprint Robotics on the industrial outskirts of this city, a house frame – complete with windows, plumbing, insulation and electrical wires – is chiseled in large panels by computerized machines in about a day. The pieces of walls, floors and roof are then trucked to the construction site to be assembled in several more days. Although drywall and other features must still be added, the process – which has been used in Europe for decades – can shave the time to build a house by as much as half.
A new generation of prefabricated housing that bears little resemblance to the modular homes of old is among several technologies homebuilders are embracing to cope with the worker shortage. They’re also starting to deploy bricklaying robots and software programs that allow them to avoid miscommunication and delays.
“We’re at a tipping point where it’s finally just gotten too expensive to build the old-fashioned way,” says Margaret Whelan, CEO of Whelan Advisory and an investment banker for the home building industry.
Many construction workers left the field during the housing crash. Baby boomers are retiring in droves. Immigrant workers face new government crackdowns. And few high school graduates are choosing a career of back-breaking labor.
Last year, at least half of homebuilders reported a serious shortage of framing crews, carpenters, bricklayers and other tradespeople, according to a survey by the National Association of Home Builders. The worker deficit is a big reason NAHB counted a four-month supply of existing homes in April, below a balanced six-month inventory. The limited stock is crimping home sales and has helped drive up national home prices nearly 50 percent since 2012, according to the S&P CoreLogic Case-Shiller index.
The emerging builder strategies already seem to be paying off, at least to some extent. Despite the labor crunch, 910,000 single-family homes are expected to be built this year, up from 851,000 in 2017, NAHB says. Yet there’s demand for 1.3 million, says Robert Dietz, the association's chief economist.
While hundreds of factory-built homes have been put up the past couple of years, up to 20 percent of houses could be prefabricated in five years, says Stephen Kim, a senior housing analyst for Evercore ISI, a research firm. And factory workers earn 30 to 50 percent less than construction craftspeople, he says.
“I think this will be a significant change in the way houses are built,” he says.
The industry is due for a fresh approach. While U.S. productivity, or output per labor hour, rose an average 1.76 percent a year from 1995 to 2015, productivity in construction declined an average 1.04 percent during that period, according to an Evercore analysis of government and McKinsey Global Institute figures. Contractors are vulnerable to weather, human error and the missteps that result when dozens of unrelated subcontractors join forces to cobble together a home.
The factory-based builders aren’t producing the kind of modular houses that have been around for decades – three-dimensional chunks of finished home pieces that are shipped to building sites in limited varieties. The new manufacturers, who serve as suppliers to traditional builders, make flat panels and can churn out any blueprint the builder requests.

Photo shows Oscar Bonilla processing lumber, which will be used to assemble floor panels on a factory production line. The machine selects from multiple tools on a robotic arm to process the lumber with millimeter precision. (Photo: Nick Panetta, Blueprint Robotics)
Building a house frame in a day
At Blueprint Robotics, about 30 software engineers and architects convert builders’ plans into programs that computerized machines follow. The machines, robots essentially, cut wood to length, form holes and grooves for electric sockets and wiring, nail the wall studs together at precise intervals and then add bigger holes for windows and doors, along with a particle-board-like sheathing.
Tasks that could take traditional workers an hour or more are completed in minutes. The factory crackles with the familiar sound of sawing, hammering and drilling, but it’s mostly machines making them. About 35 workers in blue sport shirts are scattered throughout the 200,000-square-foot plant to assist rather than toil, starting up machines and loading panels.
Machines tilt walls upright and move them on a conveyor to stations where workers briskly add wiring, pipes and windows. A robot shoots insulation into the spaces between studs. A similar process cranks out floors. A walk through the factory is like watching a house being built horizontally, with wood facades lined up in neat rows at the end.
At the construction site, it takes about a week for a crane and seven Blueprint workers to lift the panels into place and bind the frame together so the homebuilder can complete the house. The homebuilder then takes over, finishing the house the usual way by adding features such as drywall, kitchen counters and carpet.
Of the on-site improvisational method that still dominates home construction, Blueprint CEO Jerry Smalley says, “Would you have your car built that way?”
New Jersey custom home builder Robert Kiejdan recently hired Blueprint to help put up a 2,700-square-foot house in Margate. He says it normally takes his subcontractors up to six weeks to construct the shell that Blueprint turns out in eight days. After factoring in weather and other delays, he estimates the house will be completed in three months instead of the usual six.
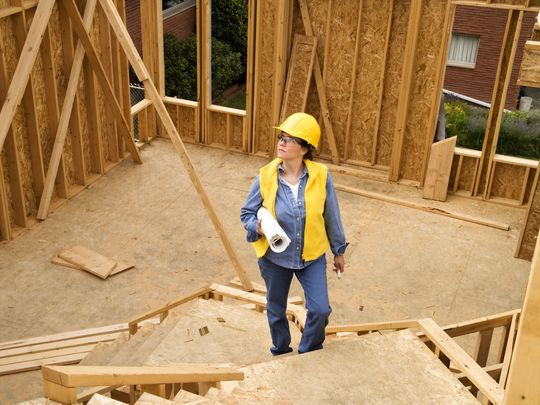
Many do-it-yourself home-building kits can be custom designed. It’s not a one-size-fits-all business. (Photo: Getty Images)
Although Kiejdan says he’s paying about 15 percent more for that shell, he’ll offset the cost by selling the house more quickly, improving his cash flow and saving on property taxes and interest. More important, he says, “It frees me up” to build other homes. He figures he can put up five houses a year with Blueprint’s help instead of two to three.
Entekra, based in Ripon, California, uses a similar computerized factory to stitch together a house frame but doesn’t add the plumbing, wiring and insulation. But because machines, unlike workers, trim walls and floors to exact lengths, cabinets and other fixtures can be crafted before the house frame is done, slicing building time by a month in total, CEO Gerard McCaughey estimates. Robots "don’t have a bad day. They don’t have a hangover.”
Entekra, which can build 500 house frames a year, is targeting large-volume builders and plans two more California factories by 2020 that can produce 6,000 frames annually.
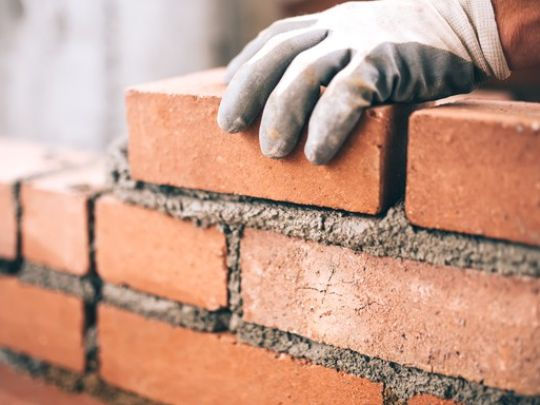
Other technologies:
Bricklaying robot
Construction Robotics of Victor, New York, has developed a bricklaying robot known as SAM – Semi-Automated Mason – that can lay 2,000 to 3,000 bricks in an eight-hour day compared with 400 to 600 for a human mason. Last year, it erected the brick façade of the lower floors of a 180-unit apartment building in Chicago.
“It’s more productive,” says Jim Weyer, president of Richards and Weyer, the masonry company for the project. The firm was able to use just two bricklayers instead of seven, cutting costs despite the $2,900 weekly rental fee for SAM.
Construction Robotics executive Zak Podkaminer says other multifamily builders are lining up. And single-family homes are a possibility, though smaller facades would be built in factories.
Construction management software
Building a house is a study in chaos, with a contractor bringing on dozens of subcontractors in a kind of ballet that’s anything but graceful. If rain delays framing by a few days, that pushes back the door and window crew, the drywall team and everyone down the line. Calling all the players to relay changes often results in missed messages. And if tradespeople show up the wrong day, they may not be available on the right day, further snarling construction.
Management software connects contractors and subcontractors to the same schedule, says Felix Vasquez, CEO of Hyphen Solutions, a provider of software used in 27 percent of housing starts last year. If framing is delayed, a manager clicks a button that pushes back the tasks of other subcontractors, who receive alerts.
Besides modestly speeding construction, the program can let a manager oversee about 25 projects simultaneously instead of 15, estimates Jonathan D’Urso, an executive for K. Hovnanian Homes.. Last year, it let the company build perhaps a few dozen more homes, he says.
“We're making fewer mistakes,” D’Urso says.